Top
10
Terms
and
Abbreviations
for
Metal
Hose
You
Should
Know.
The
goal
of
a
game
of
basketball
is
simple:
get
the
ball
into
the
hoop
to
score
your
team
points,
and
the
team
with
the
most
points
at
the
end
of
the
time
wins.
Pretty
easy
right?
On
the
surface
the
game
is
very
simple,
and
can
be
easily
understood
by
just
watching.
But
the
more
you
dig
into
it,
the
more
you
see
and
understand
all
the
nuances
of
the
sport
that
make
it
exciting
and
interesting
to
watch
and
play.
All
of
these
idiosyncrasies
have
names
and
acronyms
to
describe
them,
which
make
it
easier
for
a
group
of
fans
or
athletes
to
communicate
(read:
yell)
with
each
other.
But
for
those
of
us
who
are
not
so
familiar,
myself
included,
listening
to
a
conversation
between
a
bunch
of
super-fans
can
start
to
sound
like
a
foreign
language
and
can
quickly
get
confusing.
This
is
all
very
similar
to
the
hose
and
piping
world,
where
those
who
have
been
a
part
of
the
industry
a
long
time
begin
to
take
for
granted
all
the
terms,
acronyms,
and
abbreviations
that
we
use
on
a
daily
basis.
Not
all
industrial
distributors
have
a
familiarity
with
all
hose
types,
and
even
the
most
scrupulous
end-user
can’t
know
everything
about
every
component
in
their
plant…that’s
why
they
need
us!
So
without
further
ado,
let’s
lay
out
the
top
ten
industry-specific
terms
and
phrases
that
you
need
to
know
about
metal
hoses:
-
Corrugations
One
of
the
biggest
differences
between
metal
hoses
and
their
rubber
counterparts
is
that
metal
hoses
have
to
use corrugations to
flex.
Because
of
their
material
properties,
rubber
hoses
are
able
to
be
shaped
into
a
straight
tube
(like
a
garden
hose)
and
flexed,
whereas
a
metal
tube
would
be
rigid.
In
order
to
make
a
metal
tube
flexible,
we
manufacture
many
little
crests
and
valleys
into
the
metal
tube
which
give
it
the
ability
to
flex.
-
I.D.
ID
stands
for
the
“Internal
Diameter”
of
a
hose,
and
is
also
generally
referred
to
as
it’s
“size.”
If
you
were
to
look
down
the
barrel
of
the
hose,
you
would
see
that
there
is
a
significant
difference
between
the
internal
diameter
of
the
hose,
and
the
outer
diameter
(OD)
of
the
hose.
The
ID
is
the
one
we
use
to
determine
the
size
of
the
mating
fittings.
-
Braid
Braid
is
the
woven
strands
of
metal
wire
that
we
put
over
the
top
of
a
corrugated
hose
to
give
it
the
ability
to
handle
pressure.
When
a
tube
is
corrugated
and
made
into
a
hose
and
then
pressurized,
it
wants
to
extend
back
into
a
tube.
The
braid
prevents
this,
and
acts
like
a
trap
that
tightens
as
the
hose
tries
to
extend,
and
gives
it
the
ability
to
withstand
the
pressure!
Remember
that
steel
braid
on
a
hose
is
not
unique
to
metal
hoses,
and
often
Teflon
hoses
with
stainless
braids
are
often
mistaken
for
their
metal
hose
counterparts.
-
Cap
Welds/Braid
Collars
We
perform
2
welds
on
metal
hose
assemblies
to
attach
the
end
fittings,
the
first
is
called
a
“cap”
weld
to
make
sure
that
the
braid
wires
are
all
fused
together
on
the
end
of
the
hose.
To
ensure
this,
we
put
a
small
metal
collar
over
the
end
of
the
hose,
and
gently
crimp
it
on.
The
braid
collar
holds
all
the
wires
neatly
and
tightly
to
the
hose,
and
allows
us
to
properly
capture
all
the
elements
in
the
welding
process.
This
also
makes
our
second
fitting
attachment
weld
much
easier,
and
overall
much
higher
quality,
because
we
are
dealing
with
two
homogeneous
elements
(the
fitting
and
the
cap)
instead
of
all
the
braid
wires
and
the
hose. Never use
tools
like
a
wrench
on
a
braid
collar
(which
is
located
just
below
the
fitting)
as
it
will
damage
the
assembly.
-
O.A.L.
OAL
stands
for
“Overall
Length”
of
a
hose
assembly.
There
are
several
different
lengths
that
we
define
for
hose
assemblies,
but
OAL
is
generally
the
most
important
because
many
hose
applications
are
operating
within
a
defined
space.
The
OAL
is
the
total
length
of
the
hose including
the
fittings, all
the
way
out
(including
the
threads)
to
each
end.
The
only exceptions in
the
case
of
an
elbow,
in
which
we
measure
only
to
the
centerline
of
the
elbow,
or
with
seated
fittings
(like
a
JIC)
that
are
measured
to
the
seat.
It’s
also
common
for
a
customer
or
a
drawing
to
specify
a
length
in
a
non-standard
way,
so
take
care
to
understand
how
an
overall
length
is
being
described.
-
Live
Length
The
live
length
of
a
hose
assembly
is
the usable length
measurement
of
the
assembly.
The
corrugations
in
a
metal
hose
are
what
allow
it
to
flex,
so
anything
that
isn’t
corrugated
is
not
flexible
or
part
of
the
“live
length.”
Fittings
and
braid
collars
are
two
good
examples
that
are
on
all
assemblies
and
not
included
in
live
length.
Live
length
helps
us
calculate
if
there
will
be
enough
flexible
hose
in
the
application.
-
P.S.I.
Stands
for
“Pounds
per
Square
Inch”
and
is
a
unit
of
pressure,
an
important
performance
characteristic
for
all
hoses.
There
are
many
units
that
can
be
used
to
gauge
pressure,
but
PSI
is
the
most
common
in
the
domestic
hose
industry.
A
huge
number
of
factors
affect
a
hoses
ability
to
withstand
pressure
including
hose
geometry,
material
type,
reinforcement
braids,
and
material
thicknesses.
PSI
is
a
function
of
the
inside
area
of
the
hose,
which
is
why
very
small
hoses
handle
much
higher
pressures
and
larger
ones
are
much
lower.
More
space
inside
to
spread
over
means
lower
overall
pressure!
-
“Male
Nipple”
vs.
“Weld
Nipple”
One,
if
not
the
most
common, fitting
that
we
use
is
the
standard-threaded
male pipe
nipple.
There
are
so
many
ways
to
describe
this
fitting:
“MNPT”
or
“Male
NPT,”
“male
nipple,”
etc.
but
sometimes
can
also
be
referred
to
as
a
“Weld
Nipple.”
Fittings
suppliers
may
describe
it
this
way
because
they’re
describing
how
the
base
of
the
fitting
will
be
attached
to
the
hose
or
other
component,
whereas
a hose
supplier is
going
to
describe
the
fittings
based
on
how
the hose
assembly will
mate
with
the
surrounding
piping.
Both
are
standard
pipe
fittings,
but
when
it
comes
to
hose
assemblies
“weld
nipple”
is
not
appropriate
to
describe
the
threaded
version
of
the
fitting
and
can
cause
confusion,
and
usually
refers
to
a
plain
pipe
fitting
that
is
completely
un-threaded.
-
Alloy
Just
like
all
other
piping
components,
hoses
can
be
manufactured
from
a
variety
of
different
metals.
Hose
Master
makes
hose
out
of
321,
304,
316,
and
C276
to
name
a
few!
Each
of
these
is
an alloy,
which
is
a
mixture
of
different
metals
and
elements
that
give
the
steel
different
characteristics
and
performance
attributes
that
make
them
ideal
for
one
application
or
another. Choosing
the
right
alloy
is
critical
for
nearly
all
applications!
-
Axial
(movement)
Hoses
are
generally
used
only
because
a
hard-piped
connection
is
not
feasible.
Because
metal
hoses
are
made
for
movement,
it’s
important
to
recognize
that
they’re
not
suitable
for all types
of
movement,
namely,
axial
movement.
Axial
movement
could
be
described
as
compression
and
extension.
Imagine
a
hose
assembly
installed
straight
between
two
points.
If
the
hose
is
compressed,
the
braid
becomes
loose
and
it
can
no
longer
hold
pressure.
If
the
hose
is
extended,
it
strains
the
braid
wires
and
the
hose
itself
and
can
fracture
the
fitting
attachment.
(Check
out this
video for
more
info
on
proper
installations
and
movement)
*Honorable
mention:
Any real hoser
will
notice
right
away
that
I
left
out
the
grand-daddy
of
them
all: STAMPED.
A
special
hose
industry
acronym
that
helps
everyone
remember
all
the
critical
pieces
of
information
necessary
for
a
proper
hose
assembly
design,
but
is
too
long
to
describe
here. Click
here for
details
on
STAMPED
and
more
information
on
building
hose
assemblies.
These
top
ten
terms
and
abbreviations
are
a
good
start
for
anyone
that’s
going
to
be
dealing
with
metal
hoses.
But
hose
assemblies
are
deceptively
complex,
and
the
experts
at
Hose
Master
are
here
to
assist
with
properly
designing
hose
assemblies
for
nearly
any
application.
For
more
information
on
terms
and
definitions, click
here,
or
call
us
at
216-481-2020
or
email
us
at insidesales@hosemaster.com and
we
will
be
happy
to
assist
you! Be
sure
to
follow
us
on LinkedIn and subscribe to
our
Insights
Blog
for
regular
updates!
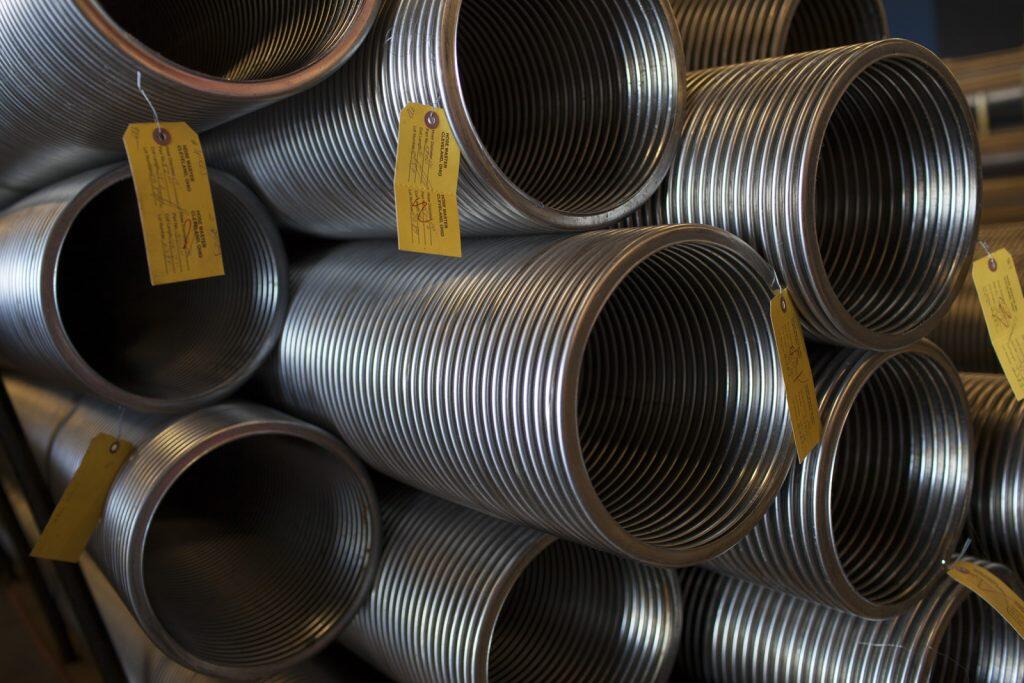
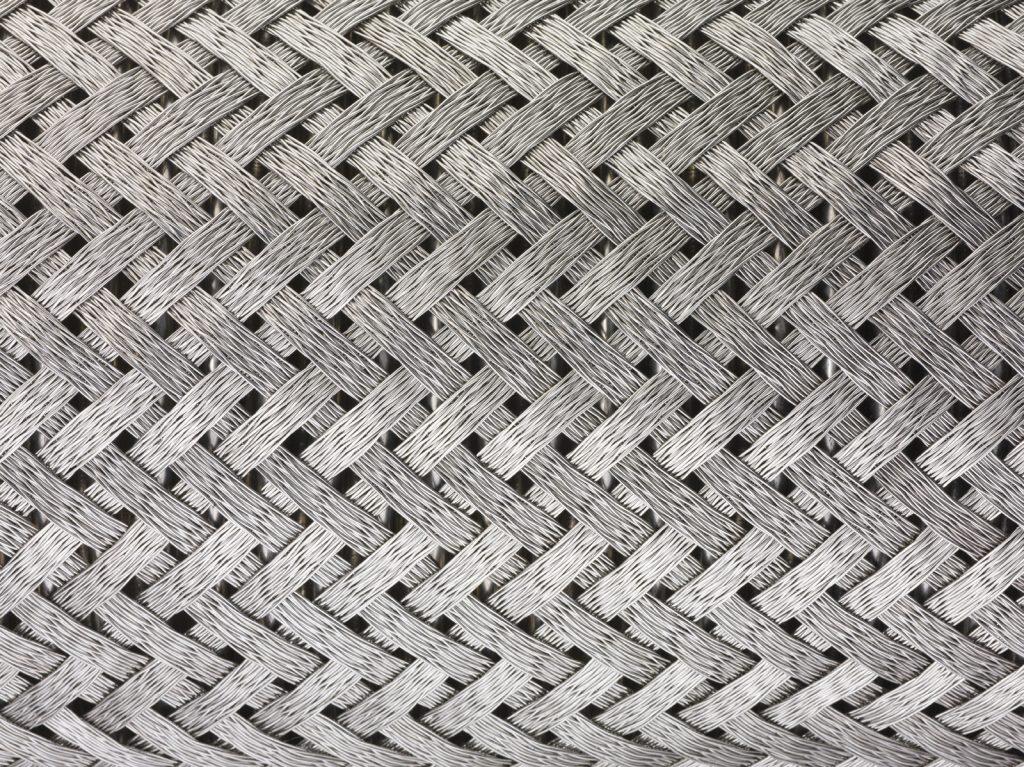
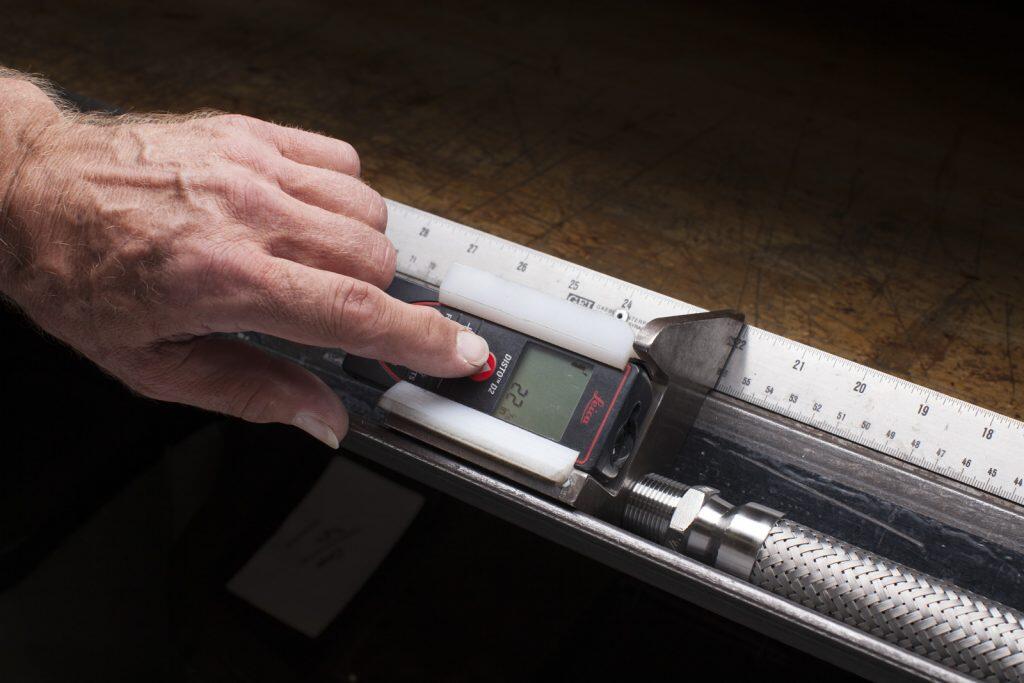
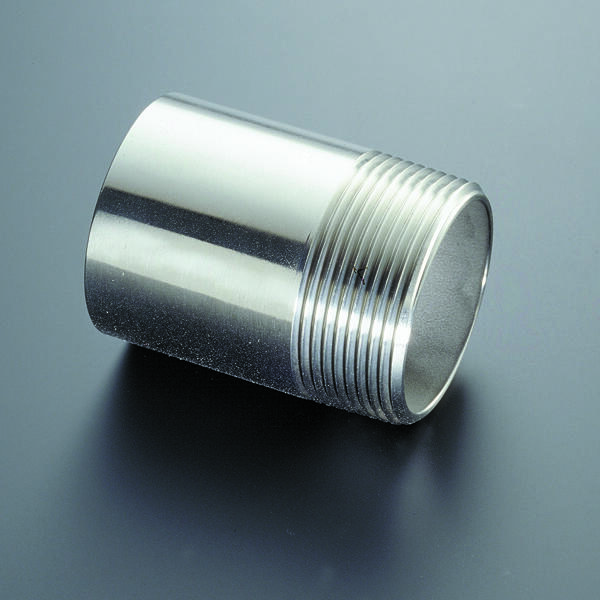
Copyright
2018,
Hose
Master,
LLC
All
Rights
Reserved