Should
you
use
a
PTFE
liner
inside
a
corrugated
metal
hose?
We
get
various
requests
from
our
customers
for
non-traditional hose
assembly
constructions that
they
believe
will
help
them
solve
tough
application
problems.
Over
the
years,
we’ve
seen
a
lot
of
these,
and
some
are
pretty
inventive,
even
if
they’re
not
the
best
solution.
Some
other
proposed
solutions
…
not
so
good!
One
especially
challenging
application
that
can
drive
people
to
consider
specialized
solutions
is
when
the
hose
is
exposed
to
corrosive
media
or
environments.
Typically,
corrosion
can
be
avoided
simply
by
selecting
an
alloy
that
is
resistant
to
chemical
attack.
However,
certain refinery applications
(such
as
those
found
in
Cokers
or
FCCUs)
entail
operating
conditions
where
some
manufacturers
recommend
a
special
corrugated
metal
hose
assembly
which
has
been
fitted
with
a liner made
from
smooth
PTFE
tubing.
While
this
special
construction
sounds
good
in theory,
it
can
create
more
problems
than
it
solves.
Let’s
take
a
closer
look
at
PTFE-lined
corrugated
hoses.
Why
consider
installing
a
PTFE
liner
inside
a
corrugated
metal
hose?
First
of
all,
regular
PTFE
hoses
offer
advantages
that
cannot
be
denied;
they
are
chemically
resistant,
they
can
be
used
for
the
transfer
of
food-grade
materials,
and
they
have
excellent
non-stick
properties.
However,
there
are
certain
applications
where
a
PTFE
hose
doesn’t
provide
the
durability
that
a
metal
hose
can
offer,
so
a
compromise
is
made
by
inserting
a
smooth
PTFE
tube
inside
of
a
corrugated
metal
hose,
and
flaring
the
PTFE
tubing
out
over
the
face
of
the end
fitting (typically
a
pipe
flange
or
some
type
of
sanitary
connection).
The
companies
offering
these
assemblies
make
various
statements
regarding
their
operating
capabilities.
Some
state
that
these
liners
can
handle
up
to
30”
of
vacuum,
can
accommodate
food-grade
media,
and
help
to
prevent
any
escape
of
the
media
should
the
PTFE
liner
fail.
The
PTFE
is
also
purported
to
have
excellent
resistance
to
large
temperature
fluctuations,
although
it
has
a
limited
temperature
range
as
we
will
discuss
below.
What
to
watch
for:
There
are
a
number
of
concerns
that
must
be
taken
into
consideration
before
using
a
corrugated
metal
hose
with
a
PTFE
liner.
-
Pressure
build-up
outside
of
the
PTFE
sleeve.
When
a
PTFE
liner
is
installed,
air
is
trapped
between
the
I.D.
of
the
corrugated
hose
and
the
outside
of
the
liner.
Gases
trapped
in
this
space
can
expand
when
heated,
causing
the
liner
to
collapse,
cutting
off
flow
through
the
hose.
To
prevent
this,
a
special
port
or
weep
hole
must
be
installed
behind
the
hose
couplings
to
allow
gases
to
vent
out
of
(and
into)
the
interstitial
space
between
the
O.D.
of
the
liner
and
the
I.D
of
the
hose
as
those
gases
expand
and
contract
due
to
temperature
fluctuations.
-
Temperature
limitations.
Standard
PTFE
tube
materials
have
a
maximum
temperature
rating
of
350°
F.,
and
must
be derated for
operating
temperatures
exceeding
100
degrees
F.
Extreme
temperatures
could
cause
the
PTFE
lining
to
buckle,
especially
in
vacuum
service.
Also,
PTFE
is
not
suitable
for
cryogenic
applications.
-
Pressure
limitations.
The
PTFE
lining
typically
cannot
handle
the
full
working
pressure
of
the
corrugated
hose
in
which
it
is
installed.
Pressure
spikes
in
these
systems
could
lead
to
premature
failure
of
the
liner.
-
Fire
Safety.
Obviously,
PTFE’s
temperature
limits
preclude
it
from
being
able
to
resist
damage
should
an
unexpected
fire
break
out.
Corrugated
stainless
steel
hose
assemblies
with
welded
end
fittings
are
able
to
resist
flame
tests,
such
as
the
NFPA
testing
required
for
flex
connectors
used
in
service
stations
to
connect
the
Underground
Storage
Tanks
(USTs)
to
the
above-ground
dispensing
equipment.
In
addition
to
the
above
temperature
limits,
PTFE
has
a
melting
point
of
623
degrees
F.,
while
corrugated
metal
hoses
generally
maintain
their
integrity
at
temperatures
exceeding
1200
degrees.
-
Dimensional
variances.
It
is
important
that
the
PTFE
liner
fits
snugly
into
the
corrugated
metal
tube.
This
helps
the
PTFE
liner
resist
“ovalizing”
and
eventual
collapse
under
vacuum.
Also,
a
snug-fitting
liner
reduces
the
susceptibility
to
damage
from
flow
induced
movements,
by
preventing
the
liner
from
flopping
around
inside
the
hose.
Because
many
hose
manufacturers
have
hose
made
both
domestically
and
overseas
on
metric
equipment,
there
can
be
significant
variability
of
the
actual
I.D.
of
the
hose,
which
can
result
in
an
improper
fit
between
the
hose
and
the
liner.
Several
other
precautions
must
be
taken
during
assembly
fabrication
to
minimize
any
potential
damage
to
the
liner.
-
Flexibility
issues.
The
PTFE
lining
is
smooth
bore,
making
it
much
less
flexible
than
a
corrugated
metal
hose.
Our
standard
flexibility Annuflex products
are
more
than
twice
as
flexible
when
compared
to
the
published
Minimum
Dynamic
Bend
Radii
of
4”
through
8”
I.D.
PTFE
lined
metal
hoses.
-
Permeation.
Although
PTFE
is
a
very
chemically
resistant
material,
it
will
allow
media
to
permeate
through
the
wall
of
the
liner,
thus
exposing
the
corrugated
hose
to
the
media
being
conveyed.
This
permeation
minimizes
any
protection
the
PTFE
liner
may
offer.
While
there
are
applications
in
which
PTFE
hose
is
the
best
option,
putting
a
PTFE
liner
inside
of
a
metal
hose
may
do
more
harm
than
good.
This
lining
limits
the
pressure
and
temperature
capabilities
while
potentially
creating
other
problems
that
could
be
avoided
entirely
just
by
using
a
properly
designed
all-metal
assembly
made
from
corrosion-resistant
alloys.
If
you
have
any
questions
regarding
the
use
of
any
non-metallic
liner
in
a
corrugated
metal
hose,
talk
to
the
metal
hose
experts
at
Hose
Master.
We’ve
seen
so
many
unique
hose
solutions
(good
and
not-so-good),
we
can
provide
the
safest,
most
cost-effective
solutions
for
the
toughest
applications.
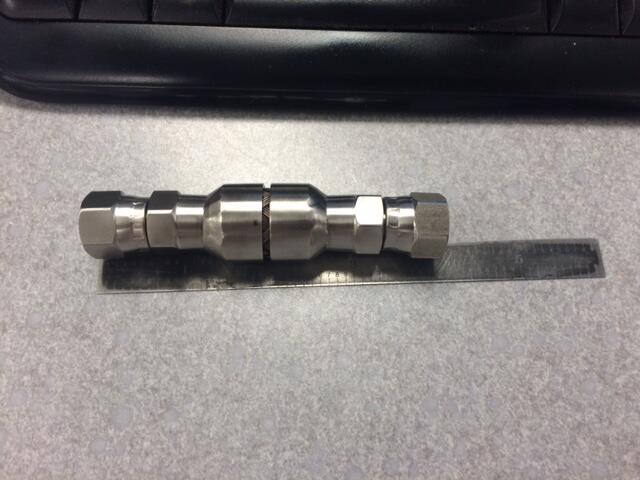
See
the
hose
peeking
out
between
the
collars?
Me
neither.
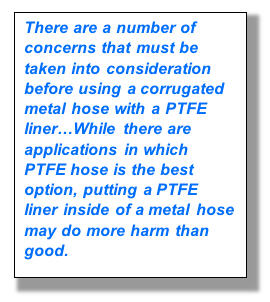
Copyright
2018,
Hose
Master,
LLC
All
Rights
Reserved